ПРОБЛЕМЫ
И ПЕРСПЕКТИВЫ ПРИМЕНЕНИЯ МЕТАЛЛУРГИИ ГРАНУЛ ДЛЯ РАКЕТНО-КОСМИЧЕСКОЙ
ТЕХНИКИ
ОАО "Композит":
Александр Вячеславович Логунов,
Александр Германович Береснев,
Алла Игоревна Логачева
Создание новых поколений двигателей,
определяющих облик перспективных изделий ракетно-космической и авиационной
техники, базируется на глубоких конструкторских, технологических и материаловедческих
исследованиях.
При этом прогрессивные технологические
решения влияют одновременно на уровень как конструкторских, так и материаловедческих
разработок, обеспечивая новые возможности реализации более высоких показателей
изделий и эксплуатационных характеристик используемых материалов.
Усложнение состава никелевых жаропрочных
сплавов, в первую очередь определяющих температурный уровень работы
двигателей и, соответственно, их эксплуатационные параметры, достигло
такого предела, когда из-за резкого развития дендритной и зональной
ликвации слитка, снижения технологической пластичности, появления трещин,
пор и других негативных факторов дальнейшее повышение свойств, а также
получение заготовок традиционными методами становится невозможным.
В сложившейся ситуации гранульная
металлургия является тем технологическим и материаловедческим направлением,
которое позволяет одновременно решать задачи эффективного производства
высококачественных прогрессивных заготовок и получения материалов с
новым уровнем требуемых свойств.
В ОАО "Композит" на протяжении
более 20 лет проводятся интенсивные исследования, связанные с реализацией
этой прогрессивной технологии.
В настоящее время на предприятии
ОАО "Композит" восстановлена и введена в эксплуатацию линия
по производству деталей, заготовок и полуфабрикатов для дисков, валов
и других узлов газотурбинных двигателей (ГТД), а также ракетных двигателей
(РД) методом металлургии гранул.
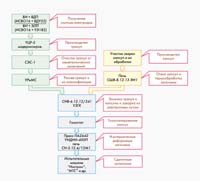 |
Схема линии по производству заготовок методом металлургии
гранул |
Ряд установок, входящих в указанную
линию, имеют принципиальные отличия от используемых в мировой практике,
что придает получаемым материалам определенные преимущества по физико-химическим
показателям. Здесь необходимо отметить, что речь идет не только об установках
ОАО "Композит", но и в целом об отечественной школе гранульной
металлургии, включающей также оборудование ОАО "ВИЛС" - создателя
ряда уникальных установок - и ОАО КБХА.
Указанное в первую очередь относится
к установкам типа УЦР, в которых получение гранул осуществляется распылением
высокоэнергетической плазмой вращающегося с большой скоростью электрода
из жаропрочного сплава (например, ЭП741НП), произведенного двойным (ВИ
+ ВДП или ВИ + ЭЛП) вакуумным переплавом, что уже на первом этапе технологической
цепи закладывает основу высокого качества гранул.
Входящая в линию установка УЦР-2
была модернизирована, и в настоящее время получаемые на ней гранулы
отличаются достаточно низким содержанием газов и других примесей. В
частности, исследования показали, что остаточное содержание кислорода
в гранулах жаропрочного никелевого сплава ЭП741НП не превышает 0,003
масс. %.
Следует отметить, что применяемая
на Западе технология распыления струи жидкого металла газом не обеспечивает
столь малого содержания кислорода, азота и водорода в гранулах, как
это позволяет делать установка УЦР.
Более высокое качество гранул в
части содержания газов и неметаллических включений, получаемых при центробежном
распылении электродов, изготовленных двойным вакуумным переплавом, может
быть объяснено двумя факторами: существенным повышением уровня рафинирования
жидкого металла, на что указывают данные, приведенные в литературе,
согласно которым количество неметаллических включений в гранулах составляет
при выплавке заготовок электродов методом ВИ - 153-328 ед./кг, методом
ВИ + ЭШП - 60-81 ед./кг и ВИ + ЭЛП - 32-38 ед./кг; более рациональными
условиями формирования капель при центробежном расположении по сравнению
с распылением жидкого металла струей инертного газа.
 |
Вид на установку УЦР со стороны камеры распыления
и плазматрона
|
Используемые в ОАО "Композит"
установки позволяют получать более 50 % гранул размером менее 105 мкм,
что в целом соответствует мировым показателям.
Следует особо обратить внимание
на роль электронно-лучевого переплава при производстве электродов. Используемая
схема получения электродов (ВИ + ЭЛП) предусматривает осуществление
операции ЭЛП на установке УЭ182, имеющей промежуточную емкость. При
этом происходит активное удаление из жидкости растворенных газов (N2,
О2) и вредных примесей (в первую очередь - S, Si, Р).
Кроме этого, в данной установке
при сливе жидкого металла в кристаллизатор осуществляется дополнительное
механическое задерживание находящихся на поверхности жидкой ванны окисных
шлаковых включений. В итоге обеспечивается заметное повышение качества
- содержание азота снижается в 2,2 раза, а кислорода - в 4,3 раза.
Другими весьма важными с точки зрения
обеспечения высокого качества гранульных заготовок являются операции
сепарации и рассева гранул. Они осуществляются на установках УРиМС и
СЭС.
В установке КРП производится рассев
гранул в вакууме и их классификация, после чего годные гранулы подвергаются
электростатической сепарации на установке СЭС, обеспечивающей извлечение
до 95 % неметаллических включений. В целом технологическая схема и используемые
установки позволяют получать гранулы, в которых содержание неметаллических
частиц не превышает 6 единиц на 1 кг.
Весьма ответственной является операция,
связанная с засыпкой гранул в капсулы и их герметизацией, которая осуществляется
на установке УЗГК. В этой установке для обеспечения хороших условий
диффузионного сращивания гранул предусмотрена их термическая дегазация
и активация поверхности путем нагрева гранул перед засыпкой в капсулы
в достаточно высоком (~ 10-5 торр) вакууме до температуры порядка 500
°С. Герметизация капсулы осуществляется путем электроннолучевой заварки
ее приемного отверстия.
Термическая дегазация гранул, движущихся
в потоке в условиях вакуума, обеспечивает заметное снижение в заготовках
не только кислорода, но также азота, соединений углерода и других элементов.
Затем заполненные гранулами и заваренные
капсулы подвергаются газостатическому уплотнению (ГИП) при температурах
1100…1220 °С и давлениях до 200 МПа.
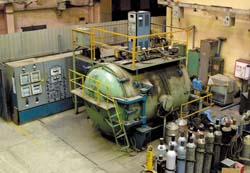 |
Установка УЗГК (СНВ-6.12) для термической дегазации
гранул в тонком подвижном слое их засыпки в капсулу и заварки |
Заключительный этап производства
заготовок - их изотермическая деформация после операции ГИП. При этом,
как показали исследования, значительно улучшаются как прочностные характеристики
(например, предел кратковременной прочности сплава ЭП741НП при 20 °С
( и20) возрастает с 1350 до 1450…1550 МПа, так и характеристики, влияющие
на надежность материала (в частности, ударная вязкость сплава ЭП741НП
при 20 °С возрастает в 1,5 раза, долговечность при испытаниях на усталость
- в 10 раз).
Следует отметить, что некоторые
эффективные конструкторские решения, направленные на создание газотурбинных
и ракетных двигателей новых поколений, связаны с получением сварных
конструкций (например, ротора барабанного типа и др.), однако известно,
что гранульные жаропрочные дисковые материалы практически не свариваются.
ОАО "Композит" разработало
новый гранульный жаропрочный сплав АЖК, который вполне удовлетворительно
соединяется аргонодуговой сваркой с помощью электродов, изготовленных
из сплава ЭП202, а также электронно-лучевой сваркой. Кроме того, новый
гранульный сплав прекрасно соединяется диффузионной сваркой со сплавом
ЭП741НП. Разработаны технологические процессы и приемы получения надежных
соединений из гранульных жаропрочных сплавов, что позволяет надеяться
на успешную реализацию принципиально новых конструкций, изготавливаемых
из этих перспективных материалов.
Необходимо указать, что применение
гранульного жаропрочного никелевого сплава ЭП741НП обеспечило в ракетостроении
создание надежных узлов турбонасосных агрегатов. Вместе с тем, дальнейшая
эксплуатация показала, что материалы этого класса должны удовлетворять
и ряду новых требований. В частности, они должны лучше сопротивляться
возгоранию в атмосфере кислорода, который при высокой температуре подается
в камеру сгорания реактивного двигателя.
В связи с этим были проведены исследования,
направленные на создание сплава с указанными качествами, и разработан
сплав НИМОВАЛ, температура возгорания которого в среде кислорода на
200°С выше, чем сплава ЭП741НП.
В настоящее время во всех странах,
занимающихся созданием авиационных и ракетных двигателей, которые работают
в условиях все более высоких температур, ведутся интенсивные исследования,
связанные с разработкой материалов на основе интерметаллидов. Только
благодаря прогрессу в области разработки технологических процессов и,
в первую очередь, гранульной металлургии, использовании аттриторов и
пр., становится возможным в дальнейшем будущем практическое использование
этих материалов.
Проведенные в ОАО "Композит"
исследования показали, что применение при производстве материалов на
основе интерметаллидов комплексной технологии, включающей использование
порошковой металлургии и газостатического уплотнения с последующим изотермическим
деформированием в условиях реализации достаточно низких скоростей деформации,
позволяет значительно увеличить их технологическую пластичность.
Совместно с И.М. Разумовским проведены
некоторые обобщения работ, посвященных анализу и разработке моделей
диффузионного огрубления структуры материала в области высоких температур.
Эти обобщения показали, что для обеспечения минимальных скоростей укрупнения
фазовых структурных составляющих целесообразно: стремиться к повышению
совершенства микроструктуры, заключающемуся в создании условий для выделения
упрочняющей фазы по возможности одинакового размера; легировать элементами,
обладающими низкой растворимостью в одной из фаз, а также элементами,
снижающими поверхностное натяжение межфазных границ. К числу последних
относятся микролегирующие элементы, локализующиеся во внутренних поверхностях
раздела - границах зерен и фаз, повышающие степень соответствия на этих
границах и, тем самым, снижающие уровень межфазной и межзеренной энергии,
ответственной за процессы коагуляции; осуществлять легирование, обеспечивающее
снижение диффузионных процессов в сплаве при высоких температурах, в
т.ч. использовать как макролегирующие элементы с низкой диффузионной
подвижностью, так и микролегирующие, снижающие диффузионную проницаемость
межфазных и межзеренных границ; оптимизировать уровень несоответствия
параметров кристаллических решеток сопрягающихся фаз.
Таким образом, можно утверждать,
что металлургия гранул является весьма эффективным процессом, обеспечивающим
одновременно как повышение качества и важнейших эксплуатационных характеристик
жаропрочных материалов, так и улучшение их технологических параметров
(деформируемости, обрабатываемости и др.).
[Напоминаем, что Интернет-вариант
статьи сильно сокращен. Ред.]