
ИНФОРМАЦИОННОЕ ОБЕСПЕЧЕНИЕ
АВТОМАТИЗИРОВАННОЙ ТЕХНОЛОГИЧЕСКОЙ ПОДГОТОВКИ
МЕХАНООБРАБАТЫВАЮЩЕГО ПРОИЗВОДСТВА
Валерий Александрович Горелов, зам. главного технолога
ФГУП "ММПП "Салют", к.т.н.
Интенсификация производства и повышение
качества газотурбинных двигателей (ГТД) и газотурбинных установок (ГТУ)
осуществляется на базе автоматизации и информационной поддержки всего
жизненного цикла изделия от разработки проектно-конструкторской документации
и технологии производства изделий до их испытаний и сервисного обслуживания.
По-прежнему значительной долей в себестоимости разработок изделий остается
технологическая подготовка производства, т.к. автоматизация и информационное
обеспечение этого этапа имеет высокую трудоемкость из-за отсутствия
необходимой технологической информации, и, прежде всего, по режимам
обработки резанием деталей из новых жаропрочных сплавов.
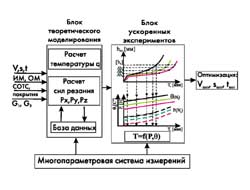 |
Функциональная схема определения
зависимости стойкости инструмента от режимов резания для пары
"инструментальный/обрабатываемый материал" с помошью
термосилового моделирования и многопараметровой системы измерений.
|
Актуальность этой проблемы также обусловлена
тем, что в последние годы в технологии производства ГТД применяются
высокопроизводительные многооперационные станки с ЧПУ, оснащенные инструментами
с твердосплавными и керамическими сменными многогранными пластинами
(СМП), как правило импортного производства. Отсутствие технологической
информации по режимам резания и стойкости инструмента при использовании
новых инструментальных материалов, упрочняющих покрытий, форм СМП и
смазочно-охлаждающих технологических сред (СОТС) для обработки резанием
деталей из жаропрочных никелевых и титановых сплавов снижает эффективность
технологической подготовки производства и не позволяет полностью автоматизировать
это процесс.
Решению проблемы установления зависимости стойкости режущего инструмента
от режимов резания и других технологических условий посвящено большое
количество научно-исследовательских работ.
Все методы расчета режимов резания, как
правило, базируются на конкретных экспериментальных данных и эмпирических
зависимостях. С помощью таких зависимостей разработаны нормативы на
режимы резания жаропрочных сплавов, на основе которых создана программная
версия по расчету нормативов трудовых затрат и режимов резания, использующаяся
на многих предприятиях.
Однако распространенные эмпирические зависимости стойкости от режимов
резания имеют весьма ограниченный диапазон использования и применимы
только для тех условий обработки резанием, при которых проводились испытания
и строилась эта зависимость. Поэтому использовать информацию о стойкости
инструмента и режимам резания для новых условий обработки деталей на
современных станках с ЧПУ мало эффективно. Таким образом, выпущенные
для предприятий отрасли более двадцати лет назад нормативы не отражают
современного уровня развития технологии и не могут являться информационной
базой для автоматизированных систем технологической подготовки производства.
Анализ конструктивных особенностей большой
номенклатуры деталей ГТД и ГТУ из жаропрочных сплавов, которые в настоящее
время обрабатываются на станках с ЧПУ, показал наличие у них торцевых,
конических, тороидальных и цилиндрических поверхностей. При их обработке
в процессе резания инструментом с постоянной геометрией и постоянной
частотой вращения шпинделя меняются главный угол резца в плане, скорость
резания, глубина обработки и т.д.
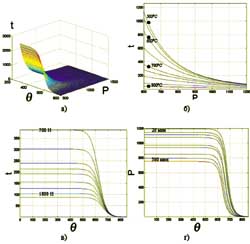 |
Пример предельной поверхности, позволяющей оценить
потури работоспособности инструмента в условиях измерения напряженного
состояния под действием силовых нагрузок с учетом температуры
резания (а); сечения поверхности линиями уровня с одним и тем
же значением температуры (б); силы резания (в); и стойкости (г),
полученной при обработке резанием никелевого сплава XH73MБТЮ инструментом
из твердого сплава
|
Цилиндрические поверхности у деталей типа
дисков компрессоров и турбин, кольцевых, корпусных деталей составляют
примерно 30 % общей площади обрабатываемых поверхностей, тороидальные
поверхности - 23 %, конические поверхности - 6 %, торцевые поверхности
- 37 %, прочие поверхности 4 %. Обработка этих поверхностей на станках
с ЧПУ сопровождается одновременным и непрерывным изменением до четырех
параметров процесса: для 43,8 % обрабатываемых поверхностей одновременно
изменяются диаметр заготовки и скорость резания, для 11,7 % - диаметр
заголовки, главный угол резца в плане и скорость резания и т.д. И только
для 29,6 % общей площади обрабатываемых поверхностей управляемые параметры
точения сохраняются постоянными.
Таким образом, выбор режимов резания в
производственных условиях является многофакторным процессом. Имея в
наличии ограниченное число исходных данных, меняющихся в широком диапазоне,
технолог должен определить режимы резания и инструмент, обеспечивающие
требования к качеству обработки детали, максимальную производительность
и минимальную стоимость обработки.
Из проведенных многими учеными исследований
и производственного опыта можно сделать вывод, что наиболее полная и
объективная оценка эффективности процесса резания может быть проведена
на основе анализа сил и температур на контактных поверхностях режущего
инструмента, зависящих от режимов резания, интенсивности изнашивания
и времени работы инструмента до установленных критериев отказа при различных
условиях стационарного и переменного контакта инструмента с обрабатываемой
поверхностью.
Чтобы иметь возможность определять эффективные
режимы обработки жаропрочных сплавов, обеспечивающих требуемые геометрические
параметры качества обработанной поверхности и физические параметры качества
приповерхностного слоя, разработана методика расчета стойкости инструмента
с помощью математической модели. При построении математической модели
стойкости режущего инструмента влияние термосиловых процессов на изнашивание
инструмента при резании определяется методами оценки поврежденности
при многоцикловом нагружении и линейным суммированием повреждений контактных
поверхностей инструмента.
Очевидно, что наибольшее влияние на износ
инструмента оказывает сила резания, при увеличении которой, скорость
изнашивания быстро растет. Можно установить какие силы и температуры
надо поддерживать, чтобы обеспечивать заданное время работы инструмента
для определенной пары "инструментальный/обрабатываемый материал".
Например, при обработке резанием никелевого сплава ХН73МБТЮ инструментом
из твердого сплава стойкость инструмента на протяжении 20 мин можно
обеспечить при силе резания 1200 Н только в случае, если температура
поверхности инструмента, износ которой является превалирующим, не превышает
580...600 °С. Увеличение силы резания вследствие, например, износа инструмента
должно сопровождаться понижением температуры.
Использование термосиловой модели стойкости
инструмента позволяет автоматизировать выбор режимов резания при проектировании
технологических процессов, поскольку дает возможность сократить до двух
число факторов, влияющих на оптимальную стойкость (с точки зрения обеспечения
заданных параметров качества обработанной поверхности), - силы резания
и температуры контактирующих поверхностей инструмента и детали. Модель,
построенная для пары "инструментальный/обрабатываемый материал",
справедлива для любой геометрии СМП и операции (перехода) обрабатываемой
детали. Кроме того, предварительные исследования показали, что для ее
построения необходимо лишь 2 % от общего числа стойкостных экспериментов,
которые пришлось бы проводить для построения традиционной эмпирической
зависимости стойкости от всех факторов, воздействующих на процесс резания.
С развитием возможностей термосилового
моделирования многопараметровые измерительные системы становятся информационной
базой автоматизации выбора условий резания для проектируемых технологических
процессов и управляющих программ станков с ЧПУ. Использование рассмотренной
термосиловой модели стойкости режущего инструмента в информационно-технологическом
обеспечении автоматизированной системы выбора режимов резания позволяет
осуществить переход от традиционных нормативов режимов резания в виде
таблиц или степенных эмпирических формул к программам анализа процесса
резания.

